How DAIKIN Plans to Drive the Use of FEP in Emerging Wire and Cable Markets
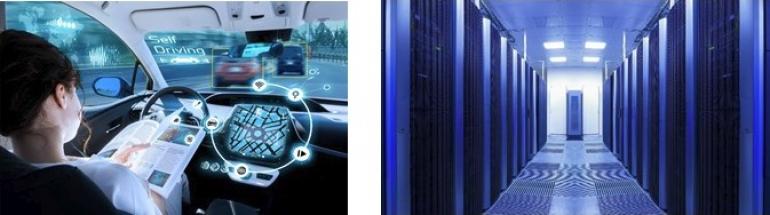
omnexus.specialchem.com
With the increasing use of data, demand for higher performance wire and cable products is exploding. Building codes in the US and Canada have driven the use of FEP as the primary dielectric insulation in commercial network cable applications due to its low dielectric constant and ability to pass strict flammability requirements.
FEP is not new, but as a leading manufacturer, Daikin provides strong technical support and product innovation to its customers. As data speeds continue to increase, the need for a high performance insulation, such as FEP will grow even in Europe where fire codes do not require it.
As a global leader in FEP production and sales, Daikin is able to quickly learn about emerging product needs from the market and responds quickly and accurately with new grades and processing technologies.
Today, we have the chance to discuss with Dan Kennefick how the use of FEP can be an innovative solution for new applications such as high speed interconnects cables for data centers and single pair Ethernet cables for automotive.
DAIKIN Relies on its Wire & Cable Experience to Deliver High Quality New Products
Regulation driven markets such Wire and Cable requires a producer to shift its focus in terms of differentiation. How would you describe DAIKIN efforts to serve the Wire and Cable market?
We live in a world where there is an ever-growing need for higher speed data and higher power usage by devices. To respond to these needs, we offer materials with excellent electrical properties and high-temperature performance. These properties are very important to support new applications such as 10GBASE-T Ethernet and PoE (Power over Ethernet).
New grades of FEP are constantly being developed by Daikin which address these market needs and in turn offer wire and cable manufacturers improved processing and reductions in scrap.
In other regions such as Europe or Asia, FEP is not a yet considered a standard wire and cable material. Do you observe a trend for more usage of fluoropolymers in the wire and cable industry?
Daikin is able to get market insights directly from customers and distributors, thanks to its strong connection to the market. Daikin has already participated in projects outside North America where FEP was used for the first time in very high-end products. Outside North America, the increased use of fluoropolymersis not yet a trend but these materials provide room for differentiation and innovation for cable producers.
We see how societal changes have led to an ever increasing need for high power consumption (PoE) by devices which challenge material producers. Where do you see new growth areas for FEP in the Wire and Cable industry?
Innovation in high technology and end user’s needs are leading to the development of higher power consuming devices. These devices are expected to be fast and support a lot a data. For example, in the very near future, we won’t need to install power wire anymore to high definition television monitors as data and power will be transmitted through the same network cable.
The choice of wire and cable materials will be driven by the need to support higher data rates, higher power, and hence higher cable temperatures. FEP is the material of choice as it has the ability to support higher temperatures than other polymers such as polyethylene or PVC for many high-power applications, such as laptop computers, LED lighting, nurse call stations, etc.
Where does DAIKIN stand on material innovation today?
We have many interesting projects in development! We are exploring new applications for FEP. One is in the automotive market for single pair Ethernet cables. As autonomous driving as a technology unfolds, vehicles will become rolling networks. Hundreds of sensors will send information to the vehicle’s main processor where split-second decisions must be made safely. Ethernet, so widely adopted in building networks, is the technology of choice to support these new vehicular networks.
The proposed single pair Ethernet cables will need to support high network speeds (multi-gigabit) and be able to endure high “under the hood” operating temperatures. FEP is best positioned as a cable dielectric material to support these requirements.